I am writing this post regarding the quality of Newmar coaches, and how the lack of quality control is currently affecting production.
In this post, I am going to show several examples of current production coaches being delivered to actual owners. I am intentionally not naming the dealers and or owners of the coach, as it is not my intent to get involved with a specific issue, but rather to discuss the overall quality of Newmar, and to make other new owners aware of poor construction. If you wish to name your coach, that is fine. Please do not name other people’s coaches. Also please refrain from naming the dealer, as the dealer is not responsible for the build and construction of the coach. This is a Newmar Corporate issue, and we need to all work together to get Newmar to listen to its owners.
Just like my campaign in 2019 to force Newmar and Freightliner to acknowledge a serious safety issue, I am once again calling on owners to act. Unless owners speak up, Newmar will have no incentive to correct the quality on the production line. Once enough owners bring up the same issue, and real costs are associated with the corrective repair, Newmar will make changes on the production to prevent future issues. This applies to all production lines of Newmar coaches, and all owners within their one-year warranty. It is especially important for those that are taking new delivery to bring this up at the time of delivery.
Do not expect Newmar or your dealer to notice this or to have resolved the problem. You are the only one that will look for quality issues and only when you bring it to your dealer’s attention will Newmar be made aware of the problem.
Why? The answer is simple economics. Most people do not notice the quality. They are looking at the coach with “rose colored glasses” and feel very intimidated by all the technology and luxury.
Newmar is balancing the cost of correcting all coach’s vs correcting only the ones that notice the quality issues and take the steps to get it corrected. You will likely be told things like “This is how they all are” or “this is acceptable”. I am giving you the information you need to push back against this, and to be armed with what is the expected quality.
It is my intention to educate the buyers of Newmar motor homes so that with one united voice we can make it very clear that poor quality will not be accepted.
WHY DID WE CHOOSE NEWMAR?
Matt Miller says it best, on the main page of https://www.newmarcorp.com
Newmar is proud to continue a half-century tradition of building motor coaches by hand, one at a time, with help from the people of Nappanee, Indiana. Individuals to whom superior craftsmanship is not a goal, but a way of life. Their obsession with quality and passion for innovation is what makes our competition feel like a compromise, which is why we say that when you know the Newmar difference, you know our people.”
– MATT MILLER, Newmar President & CEO
Hand Built Coaches built one at a time implies superior quality and craftsmanship. In fact—Matt said that in the second sentence
“Superior craftsmanship is not a goal, but a while of life”
So now we have the standard that Newmar promised us. That is why we purchased a Newmar. Newmar is responsible for all aspects of the coach it delivers. Newmar does not manufacture every component used in their motor homes. Items like electronics, air conditioning, appliances, etc. are not under the direct control of Newmar and are beyond the scope of my call to action.
I am focusing on the three areas that represent the craftsmanship and skilled labor of the Newmar coach: Exterior Paint & Body, Interior Woodwork, Tile flooring, backsplash and showers.
Exterior Paint
Newmar has a full section of their website dedicated to Paint & Exterior. You can find this on their main website by navigating to the “Why Newmar” and choosing the link “Paint and Exterior”. The page is found here: https://www.newmarcorp.com/why-newmar/newmar-difference/masterpiece-finish/
Newmar uses an automotive paint process. Those that have worked in auto body understand that there are 3 major steps. Prep – Paint – Finish.
Paint Prep
Prep is when the surface is cleaned, all foreign objects have been removed, surfaces are sanded smooth, and non-painted surfaces are taped off and protected.
This crucial step is often left to unskilled labor, or cheap labor, because it is so time consuming. All body shops use the least talented person for this prep stage. A good painter will inspect the work done in a very detailed, intense inspection covering the entire painted surface. The inspection time on a small corvette can easily take an hour if it is a full paint job. This inspection is always done by the person that will be doing the painting because “EVERY INCH MATTERS” – taken again from Newmar’s website.
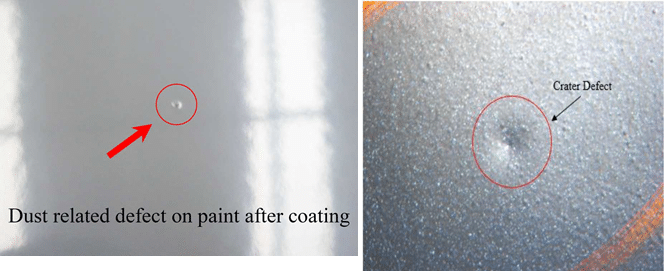
When surface prep is not done properly, dust particles end up under the paint. The coaches I have inspected from Newmar are littered with dust below the paint. These are referred to as “dust-inclusions”. Each of these should be marked and identified.
You may decide that a small percentage of dust inclusions is acceptable. I recently inspected a 2022 Luxury line coach that had 17 markings noticeable below the slides on one side. This is a 45 ft coach. That represents 37% based on linear footage of that small section—below the slides. To me, this is beyond acceptable and warrants a repair. Getting on a ladder and inspecting higher areas would give a more accurate representation of the defect rate.
Info Source: https://www.glasurit.com/uk/dust-inclusions
Painting
The process of applying paint takes a lot of skill to properly balance between not enough paint and too much paint that causes a run. My observations of many 2022 Newmar coaches are showing a drastic increase in running paint near lighting holes, corners, and other areas of the body that have a curve to them. These are spots where the person holding the spray gun, with the attached hose is having to change an angle to get paint on the surface. That change of angle is restricted by their equipment and location. Unlike automotive where chassis are dipped, or a robot with a fully articulating arm is applying the paint, humans are very limited. A skilled painter knows how to time their paint pass for these areas, and to plan the steps for each surface. The paint jobs for I have seen for 2021 and 2022 show a lot more runs than is normal. It is never acceptable to have a run in your paint and must be dealt with. This will require sanding, and additional clear coat to properly fix.
BASF describes paint runs, with a few examples in this article:
https://www.glasurit.com/uk/runs
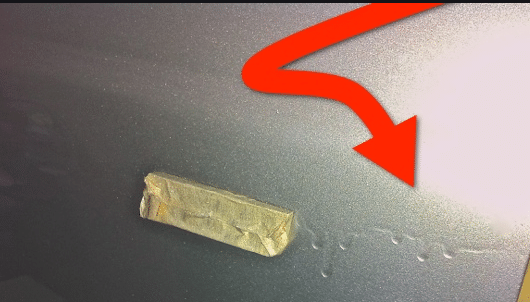
The best way to find a run is to examine every inch of your paint surface in daylight. Especially around areas where lights, doors, and other accessories attach to the surface. Cutouts for taillights, headlights, and around the curves.
Runs are a costly mistake to fix once the coach has been clear coated. The run was noticed by the painter during paint. That was the best time to correct the problem. The coach would need to dry, then the area with the run wet sanded and repainted. This takes time and stops a production line.
Newmar has made the decision to not stop or delay production to fix the problem, and to ship it as-is.
With a Newmar full body paint, there are multiple paint layers. Each layer is done with a very large template that is applied to the surface to make the tape lines easier to deal with. The process Newmar uses is very good, and I have not seen any examples of razor blade damage to the surface paint.
The final layer is the clear coat. This layer is responsible for the shine as well as protecting the paint. A proper application of clear coat will make the difference between a dull coach and one that shines. When clear coat is sprayed, it is usually put on thicker than the paint. If the painter intends to “cut and buff”, then there will be multiple layers of clear coat sprayed to add thickness for the final detailing step. A coach that does not get the cut and buff will have a very thin layer of clear coat.
The cut and buff process is also referred to as paint correction. This process is done in 1 or more stages where a compound is applied to the clearcoat and polished using pads. The number of stages determines the types of polishes and pads, and how much shine the product will have. A king Aire will always look deeper than a Dutch star due to the number of stages performed by the factory.
This is an area that Newmar has always struggled with. The cut and buff process is intended to make the coach look better, but often leaves a coach full of swirl marks that will destroy the overall appearance.
100% of all Newmar coaches are affected by this problem. It takes a trained eye to spot a swirl mark, and the correct lighting. When the lighting is correct, you will see what appears to be spider webs in your paint. Darker colors show it more than lighter colors do, but all the colors have it. I have never seen a factory painted coach leave Newmar without these swirl marks.
I have not watched the process of a Newmar coach to know when the swirl marks are getting put on the coach, and I have blamed the cut and buff for these as an assumption. It is very possible that the Newmar detail crew is responsible for these marks in their wash procedures. BASF clear coat is extremely soft and can easily take 3 months to harden properly. Washing a coach in the first 3 months should only be done with non-touch methods. Lambswool, microfiber, or any other material should never be used in the first 3 months after painting with BASF clear coats. This is where most coaches develop micro scratches and swirls.
If you notice these during your PDI— point them out and get them documented for correction. Once the swirls have been corrected, you need to make sure that only touch free washes are done until the clear coat has hardened, and you have applied a proper protection layer of either wax or ceramic coating. I will cover proper washing techniques in a separate post.
You will not be successful in seeking warranty coverage for swirl marks that you discover after your PDI. Your only recourse will be to have a 1-stage paint correction done. The cost of a single stage paint correction is between $3,000 and $6,000.
My 2019 Dutch star was factory delivered with swirl marks. I did not know enough about the issue at the time to make a proper case for warranty repair, although I did point them out. I left the factory with the understanding that they would be repairing the swirl marks but chose to have it done on my own. Here is an example of the paint swirls before repair:
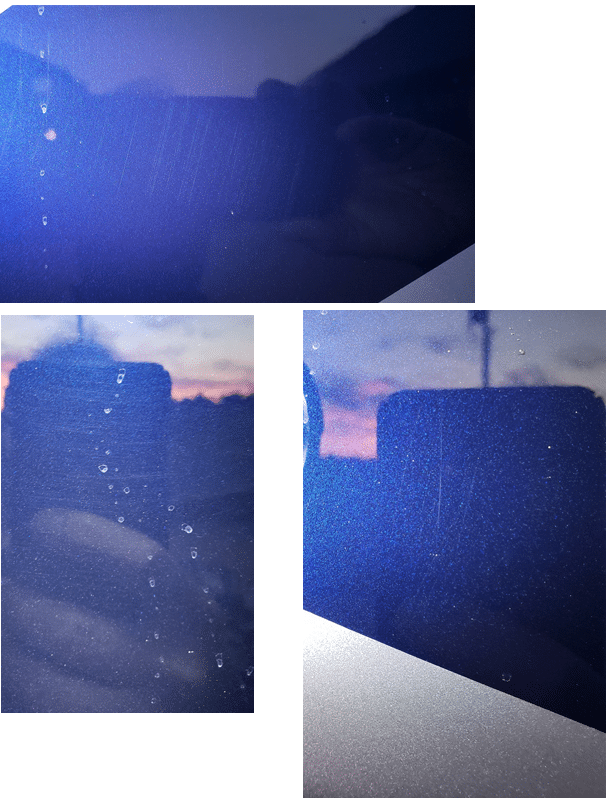
After a single stage paint correction, not only did the swirl marks disappear, but the paint itself came to life. A proper single stage or 2 stage cut and buff will give the same results, but the paint will quickly become damaged after an improper wash. Here are the results of a single stage correction.
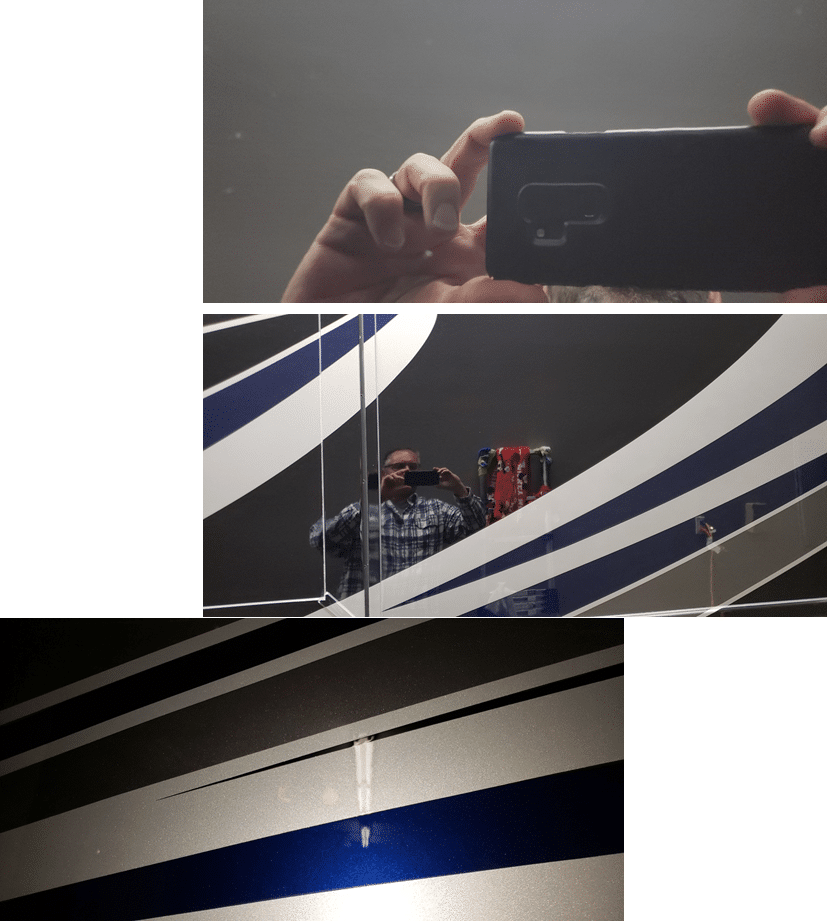
Paint – Exterior Summary
Inspect your paint. If you find runs or dust inclusions – report it to Newmar. During the first year of ownership, the warranty clearly covers these items. This will affect your resale value if your paint has these types of flaws, and it affects the overall appearance of the coach. Use painter’s tape to mark each area, and then take pictures. You can not have too much documentation.
DURING PDI – Inspect for paint swirls. Make sure you look at your coach in different angles of sun and from different distances and angles. Some micro swirls show up under direct light, and some from refracted light.
Any paint swirls found should be documented and put thru as a warranty item. If Newmar declines this work, then it is on your dealer to fix it, as they are the most likely to source of the problem and the reason Newmar is declining the repair. You will not have the option to get this corrected after you leave with your coach.
If you choose to ignore the paint swirls, be aware that it will cost a minimum charge of $3,000.00 to fix this in the future.
Interior Woodwork
One of the distinguishing features in Newmar is the custom cabinets and woodwork. This is a major reason people choose Newmar. I have always been very happy with the cabinets and overall quality of my Newmar RV’s and was excited to upgrade that experience with my 2022 London-Aire. We upgraded to the Glacier Glazed Maple wood trim to make the coach really stand out.
During my travels, I have had the opportunity to see a few 2022 Newmar RVs, both at dealerships and owned coaches. What has shocked me is the appalling quality that is being produced out of Nappanee at this time. Issues I have seen are inconsistent stain, miter joints that are not done properly, trim pieces cut too short, ceiling features not assembled properly, and nail holes lacking putty and sanding prior to finish.
If you have a Newmar coach under warranty, examine your wood closely. Look at alignment, color, grain, and overall craftsmanship. I am providing some examples of the problems I have noticed.
Here is a sample of wood for a crown molding that was cut too short. The only fix for this is to cut a new piece of wood. Anything else is patch work and should not be accepted.
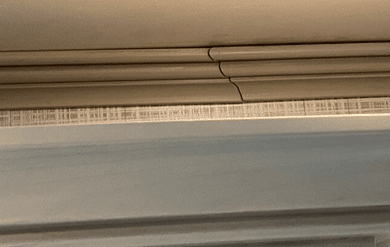
This is an example of decorative wood that was not glued properly.
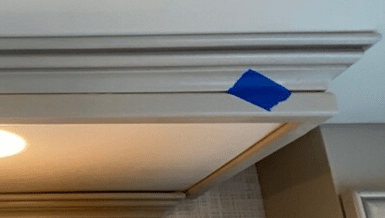
This is an example of trim that was not cut properly, and the stain does not match between the pieces. Further there is obvious damage to the wood itself.
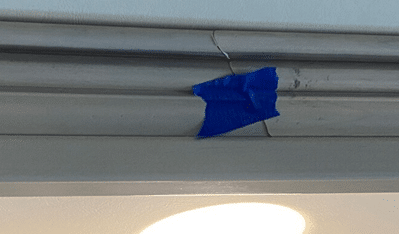
Other examples are finish nails that are not hidden:
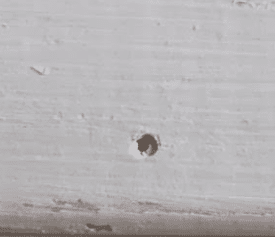
Cabinet doors not aligned:
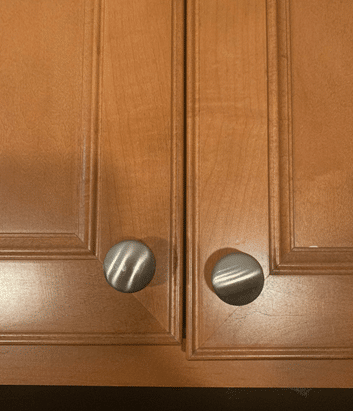
Bad Miter joints on Cabinets:
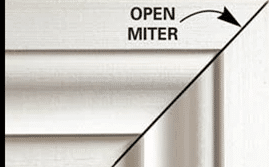
Poorly designed Miter Joints – Wood grains are not matched.
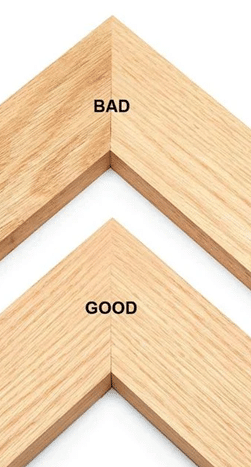
If your coach shows any of these types of defects, this needs to be documented and sent to Newmar. The only solution for most of these defects is for Newmar to replace the wood. This is a major reason why Newmar coaches have held their value so well. If Newmar quality is allowed to drop unchecked, our future resale values will suffer. For new owners, there is absolutely no reason for you to accept this kind of poor quality. It is up to you to make sure your dealer and Newmar are aware of the issue.
Tile, Back Splash, Grout
Newmar does an amazing job with their tile work. This includes back splash, showers, flooring—it is amazing. My 2013 Dutch Star had a lot of tile issues, and at that time Matt Miller and team contacted me and not only fixed my coach, but they changed a lot of internal processes. The quality that comes out of the factory since then has been as near perfect as anyone could expect. I am happy to state that this holds true today, as all the 2021 / 2022 coaches that I have looked at have had excellent tile, grout, and backsplash installations.
Due to the way Newmar manufactures the floor, doing the tile floor as the last stage in the chassis shop before construction of the house—the grout should be perfect. If you see pitting or missing grout, this should be documented with Newmar for repairs.
The shower and back splash are applied during the construction of the house. Pay close attention to tile patterns to make sure that you don’t have misaligned patterns, and that the grout lines are consistent width.
This will take a close examination, paying attention to the details. Minor imperfections may not be a big deal, but some large mistakes can easily be overlooked without close examination.
Pay attention to the caulk in the kitchen and bathroom. Make sure the bead is a consistent width, and fully covering the gaps.
Call to Action
We owe it to Newmar, the dealers, and to ourselves to make Newmar aware of the quality issues. The long-term damage that will come from acceptance of poorly manufactured RV’s will affect all of us. As owners of Newmar coaches, our investment will be lost if the product quality continues to drop. This affects us short term and long term.
Newmar has routinely increased pricing yearly, and recently multiple times per year. The justification for this increase is the additional hardships associated with labor and supply chain. For this reason alone, we must insist on the product that we are being delivered meets the very standard we have been promised.
There is a lot of power in numbers. I have personally proven this many times, most recently with the Freightliner Dash Recall that I was able to organize. It will not take long for Newmar to implement the very necessary quality control if they start seeing massive amounts customer complaints.
I think that most people have not taken the time to look for the problems that exist. Their assumption is the dealership or Newmar already did this, so it is not necessary for the customer.
The opposite is true. Only the customer is incentivized to complain. The dealer is in the middle, so they are not going to go looking for a problem. Newmar is already selling every coach they can manufacture, and they are behind on production due to supply chain. They are playing the odds game hoping that only 2% of all customers will notice these problems, and they are right. Many of the coaches that I have seen are owned by private persons already. They did not know they had a problem, and I was left struggling with how to handle the situation. Obviously, I want my coach perfect, but in the grand scheme, I want the overall quality of Newmar to remain superb.
This post is my solution to that dilemma. By documenting what you should look for, I am letting you find the issues for yourself. Once you find it, I implore you to document it and open a case with Newmar, not your dealer. Newmar needs to hear from its owners directly. They will coordinate with your local dealer for repairs.
Feel free to post your findings here. If you want information shared anonymously, send me a message and I can post additional findings. The goal is to make Newmar aware of the problems, so that it can be corrected.
Thank you for this important insight. We are at Newmar for the next few weeks to get our punch list worked out—scheduled for three weeks. We have numerous paint defects, from drips and runs to overspray as well as what appears to be beard trimmings visible in the lighter colors of our rig! ?
We also have many interior defects and poor workmanship, such as scarf joints that are too tight making the edges slip apart, and nail holes that are not filled. Also, maybe not noticed too often, the corner trim pieces that wrap the wallpapered boards together have the same decorative wallpaper glued (adhesive) to them, and the pieces they use do not wrap completely around the trim. This issue makes for poor wear and tear because every time we walk by and rub it, it gets separated and dirty.
Again, thank you so much for the smart, and calm “Call to Action”. Learned quite a bit reading your page. Sincerely…